The XLDsl accommodates up to 1008 factory-installed semi-rigid 18 GHz coaxial lines in a configuration with two pulse tubes. Its side-loading feature allows experimental wiring to be prepared away from the cryostat while the system is running.
Even with its extensive capabilities and superior performance, a fully automated cool-down sequence from room to base temperature can still be carried out at the push of a single button.
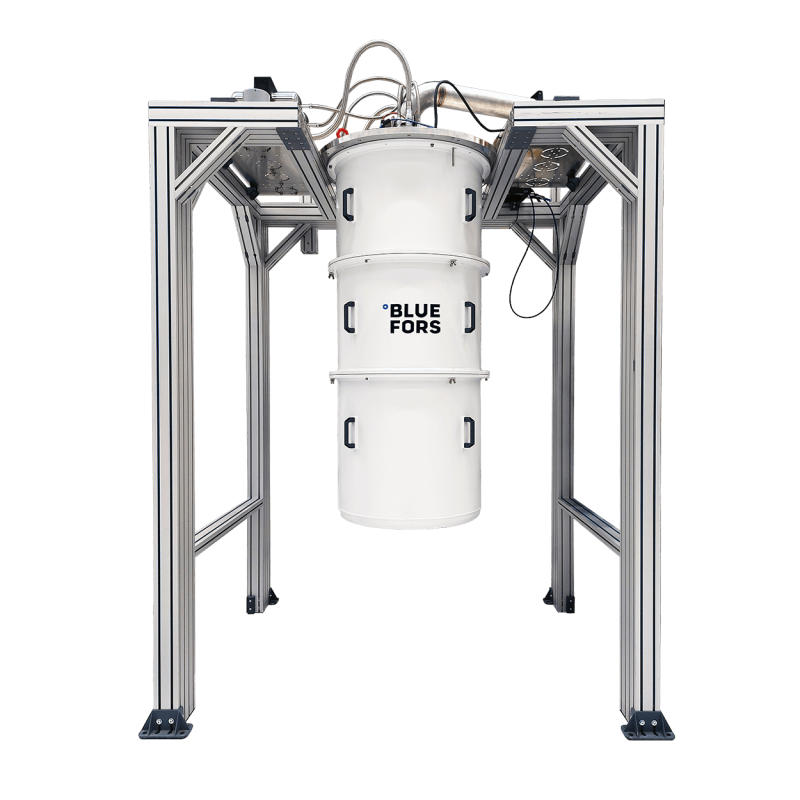
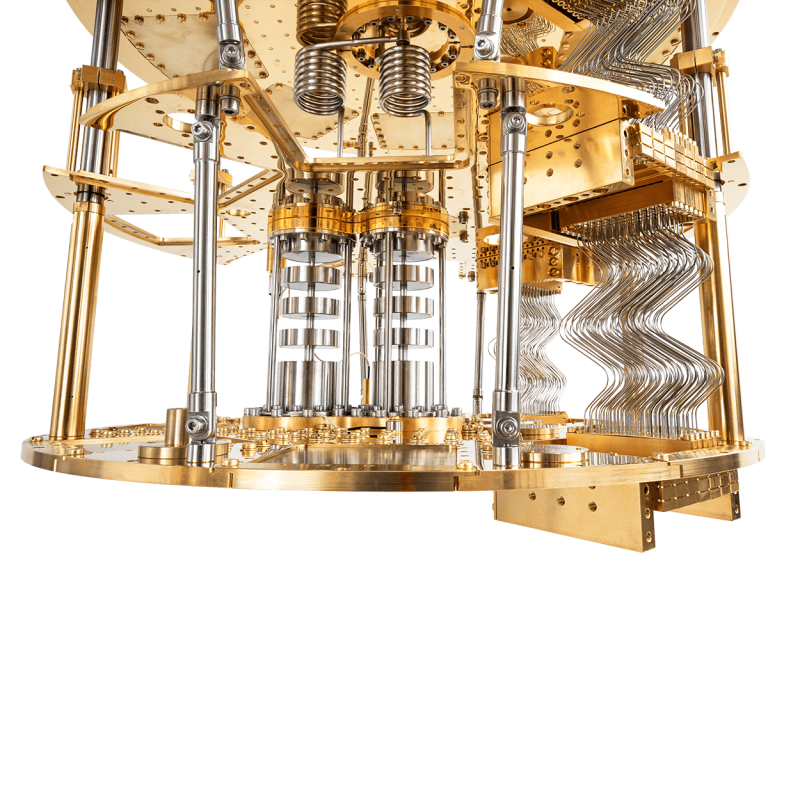
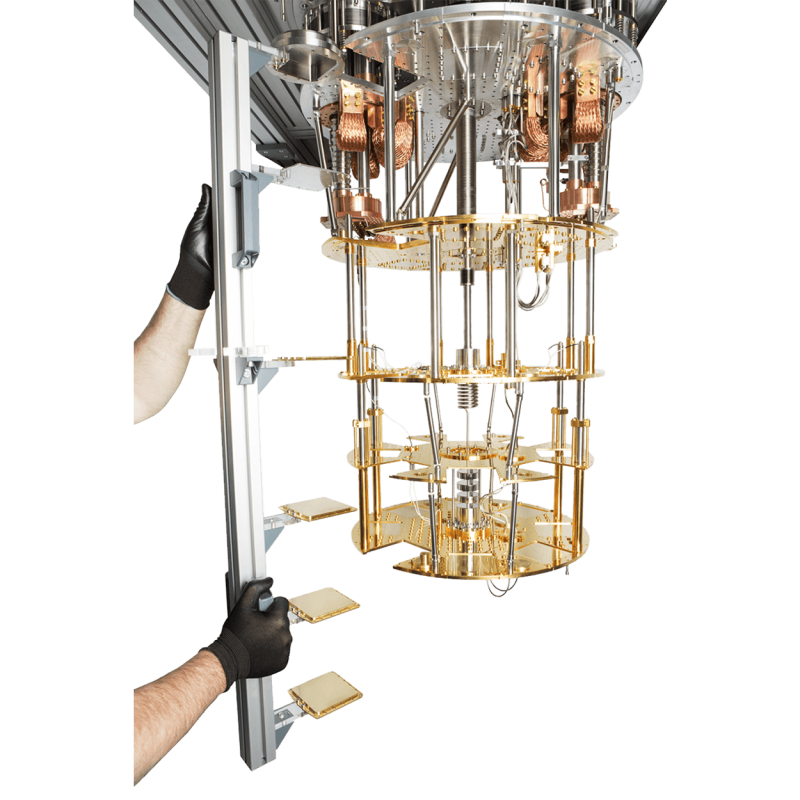
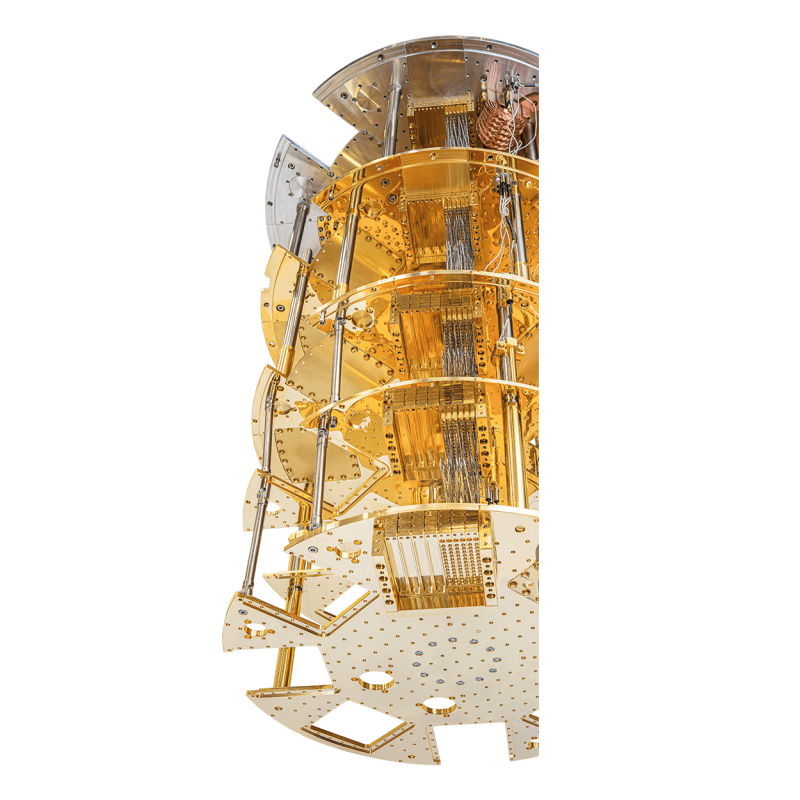

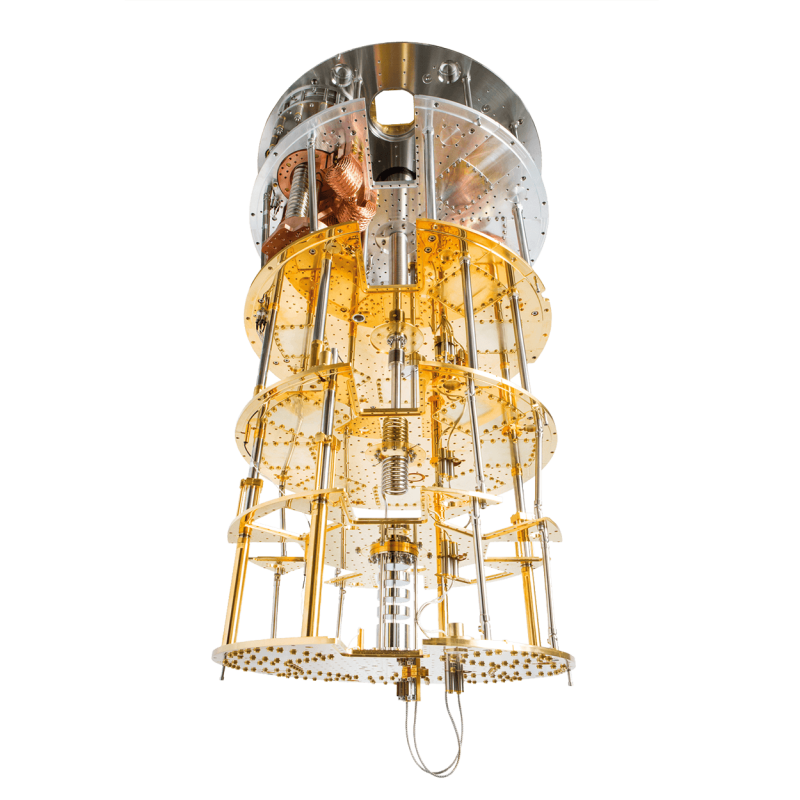
Product Highlights
1.0
XLDsl
Dilution Refrigerator Measurement System
Gas Handling System & Control Software Generation 2
Services
Total System Care
Total System Care enables you to focus on your own work – doing research and measurements. The service ensures that systems operate at the best possible performance level and with maximal uptime, without users needing to spend time maintaining the systems themselves.
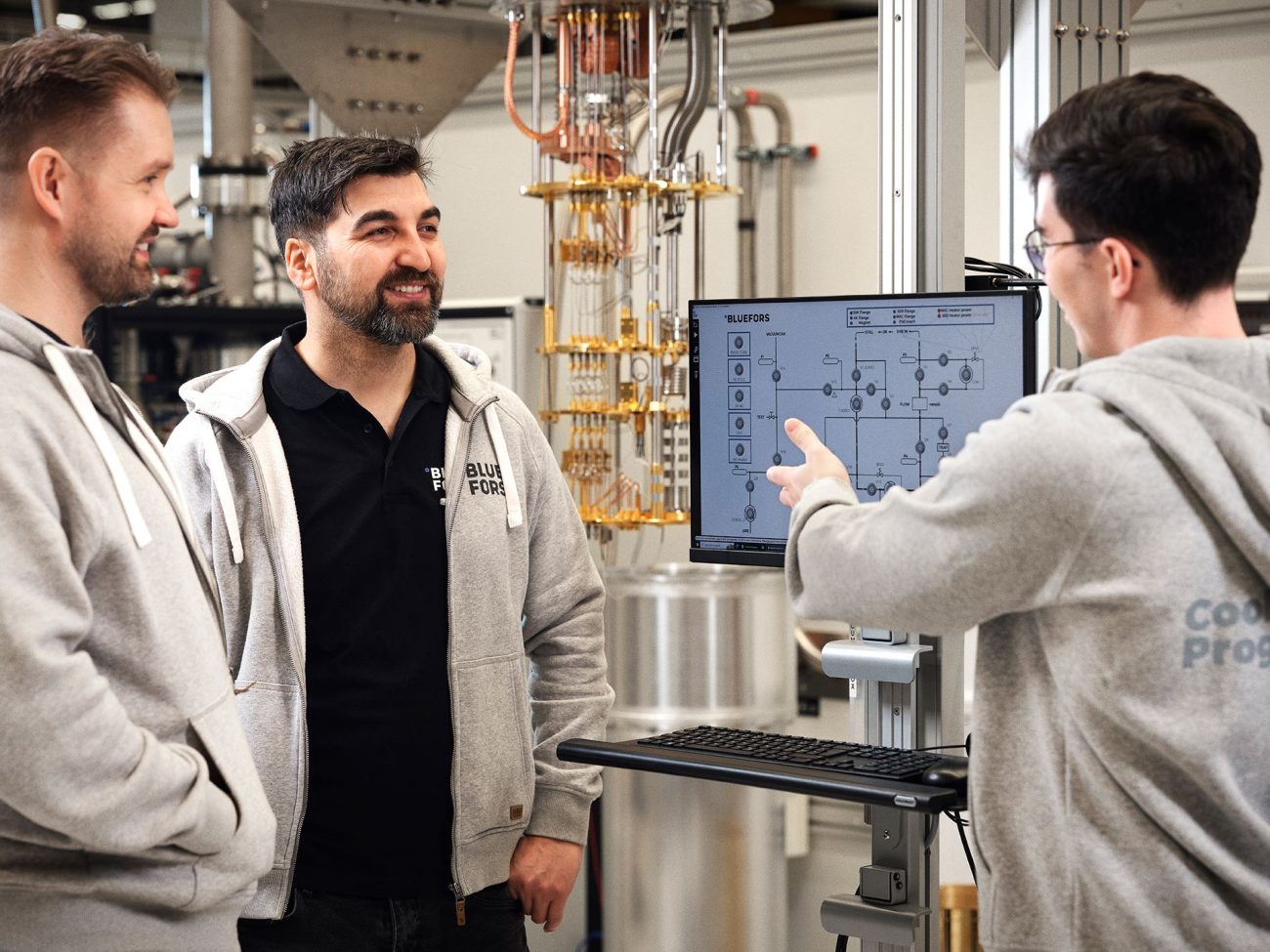
Technical Specifications
2.0
XLDsl
Dilution Refrigerator Measurement System
Pulse Tube Cryocooler Configurations
3.0
XLDsl
Dilution Refrigerator Measurement System
Options
4.0
XLDsl
Dilution Refrigerator Measurement System
Performance Graphs
5.0
XLDsl
Dilution Refrigerator Measurement System
Services
Customer Care
We support our customers throughout the lifetime of their system, providing dedicated care to find solutions for any issues. Our technicians and engineers are ready to help you wherever you are located, with prompt service delivered either remotely or on-site.
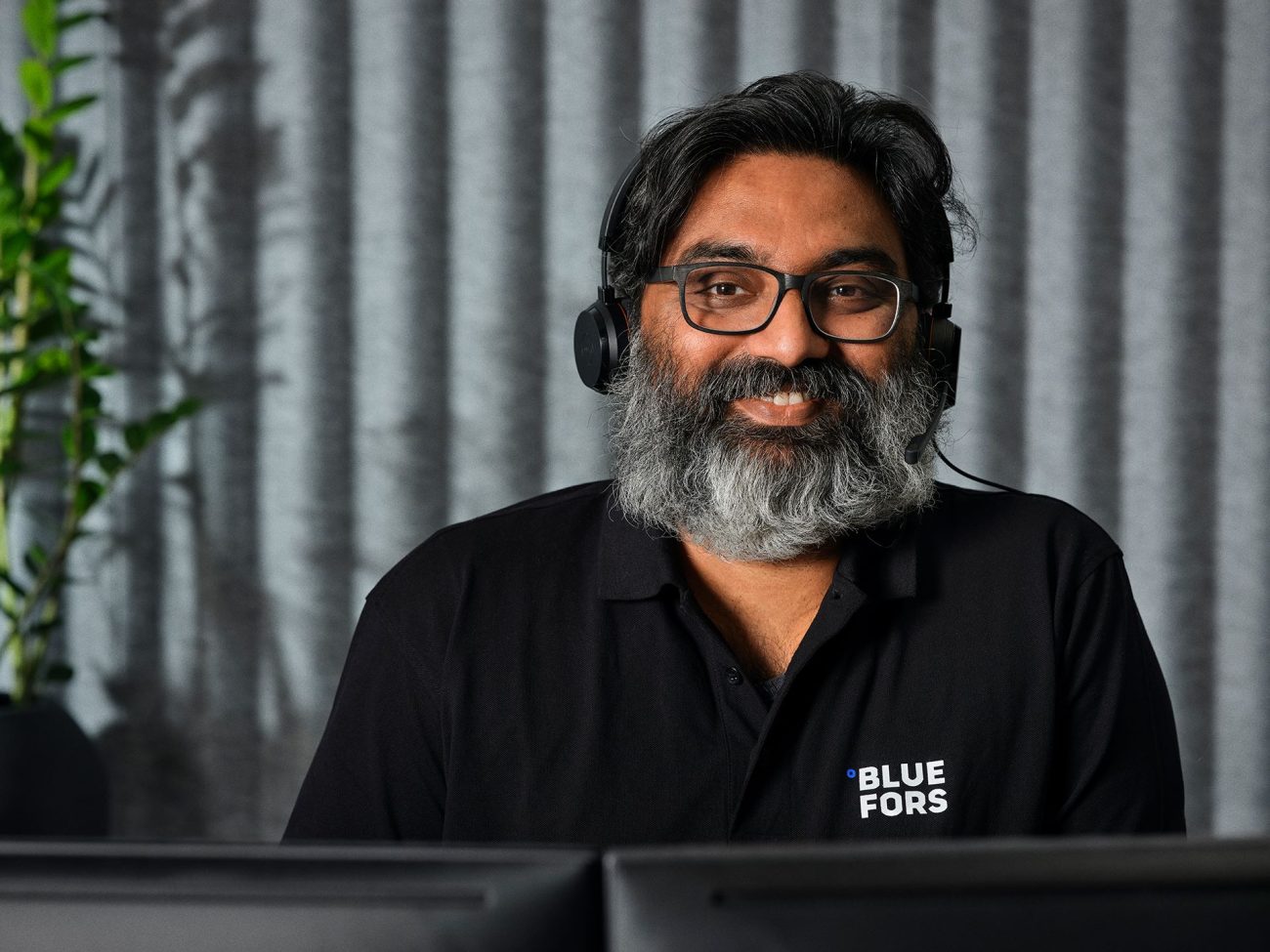
Related Products
Layout and Facility Requirements
6.0
XLDsl
Dilution Refrigerator Measurement System
See Also
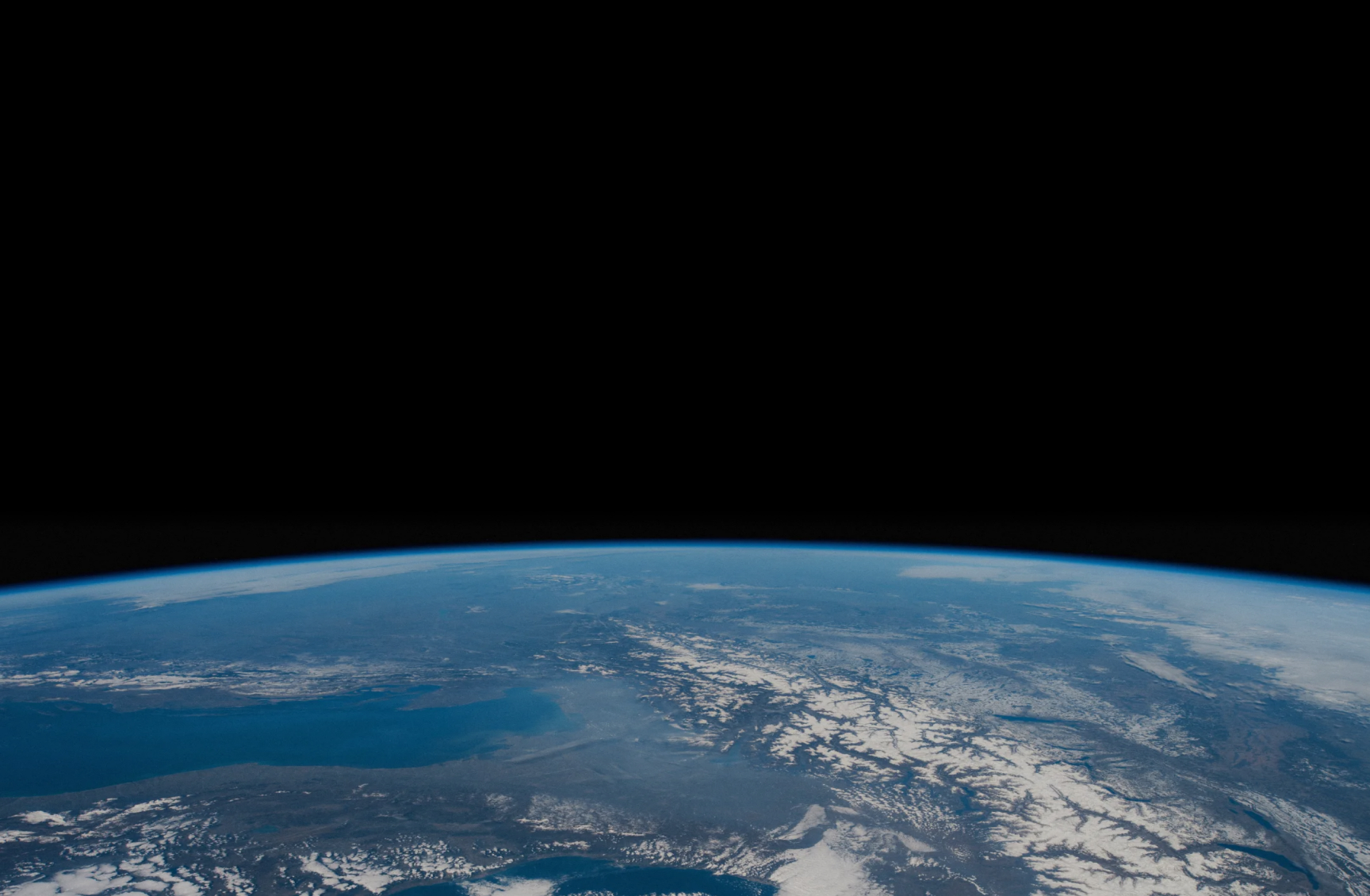