KIDE Cryogenic Platform: From Design to Delivery
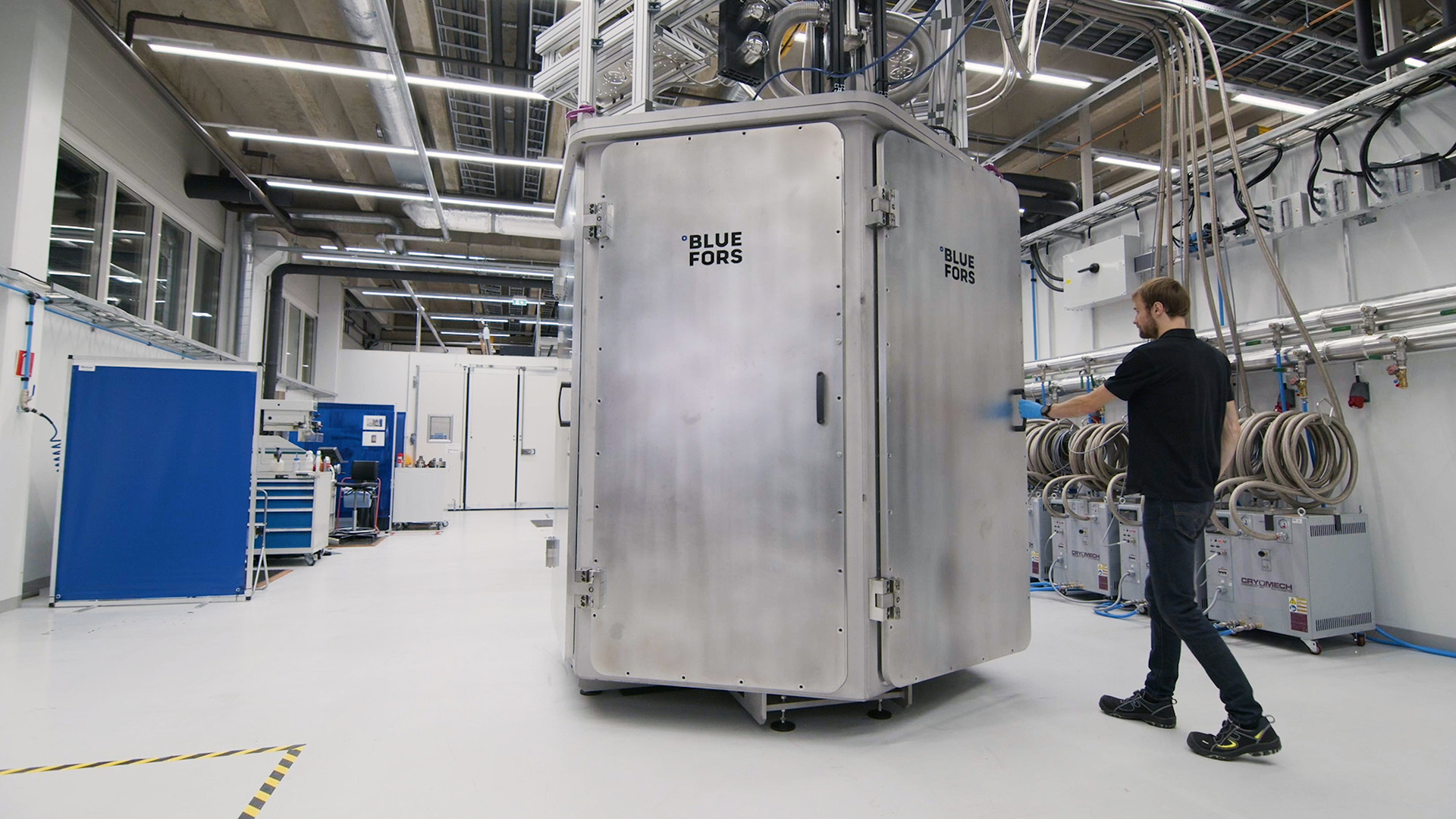
In April 2023, the first KIDE Cryogenic Platform was ready to be delivered to its new home at IBM. In this article, we take a detailed look at KIDE, and how Bluefors took it from initial concept to production-ready reality in less than two years.
Answering the Call of the Community
At Bluefors, we love to engage in active dialogue with the quantum technology community. By keeping our finger on the pulse, we can respond to the current and upcoming needs for cryogenic measurement systems and help companies and research departments make progress happen.
Around 2020, after talking with the community, we identified a growing interest in large-scale quantum computing, and specifically the need for a system that would be ready for the future, offering the cooling power and increased payload space to operate 1 000 qubits.
Which is why, in 2021, we started sketching out the first draft of ideas and designs for a new system that could meet those needs; a system that would become the KIDE Cryogenic Platform.
The Road to 1 000 Qubits (or More)
We knew from the start that this would have to be a large-scale system. But building a system ready for 1 000 qubits is not simply a matter of increasing the size of the cryostat; everything else — the cooling capacity, the wiring and measurement infrastructure, the payload area — also needs to be scaled up.
In order to facilitate 1 000 qubits, the system needed to offer the infrastructure to support that. The final KIDE design enables installation of up to 4 000 High-Density Wiring RF lines. To achieve that number, it also needs supply enough cooling power.
Every step up in power and capacity brings with it other associated challenges. How do you provide adequate maintenance access for such a complex system? How do you design enough flexibility into the system and maintain cooling efficiency? And how can you design for the future — for the possibility of scaling up to 10 000 qubits?
Unique Access to Quantum Devices
One of the most distinctive features of the KIDE Cryogenic Platform is its hexagonal shape. This design choice was grounded in a ‘form meets function’ mindset.
If a regular dilution refrigerator would simply be supersized, it would become very hard to access the cryostat and payload — removing the external cans and shields would become increasingly laborious with every scale up in size. To overcome this problem, with KIDE, access to the payload space was completely reimagined.
The entire system was designed to be built inside a self-supporting vacuum chamber with multiple access doors featuring integrated radiation shields. This would allow just one person to maintain the system and the payload by simply opening a door. It’s even possible to work inside the voluminous payload area.
However, as well as providing unprecedented user access to the infrastructure and payload within, the hexagonal design also has advantages when thinking ahead, making it possible in the future to connect clusters of KIDE units together, and potentially deliver a combined processing power far beyond 10 000 qubits.
Imagining a future-proof cryogenic solution for tens of thousands of qubits is one thing. Actually building it is another thing entirely. How would you even provide enough cooling for 1 000 qubits?
Fortunately, at Bluefors, we have some experience in this area…
Cool Qubit Solutions
Our design team approached these challenges pragmatically, reimagining how a cryogenic measurement system built for the future might look.
When it comes to cooling a system of this size, the design team needed to imagine the potential needs and uses of such a system, and how it could function. Going back to the cryogenic drawing board allowed them to find a practical solution with additional benefits.
KIDE was designed to take payloads up to 500 kg, which, in itself, dramatically raises the cooling demands. To achieve that, KIDE uses three independent dilution cooling units. During development, the team quickly understood that this delivers not only optimized payload cooling, but also, through enhanced control of the cryogenic technology, the opportunity for multiple thermally insulated temperature zones on a single flange.
The 9 Pulse Tube Cryocoolers utilized in KIDE were also given functional separation — there are dedicated pulse tubes for operational cooling, customer payload cooling, and cooling the shields. The system also makes use of a Long-Life Cold Trap, providing an optimal environment to continuously operate quantum computers for up to three years without interruption.
All these design aspects and features in combination make KIDE the ideal solution for cutting-edge quantum computing applications, both for today and in the future. Our design solutions allow KIDE to work as a stand-alone system, but also as something that could be combined with multiple KIDE systems, or bring Quantum Computing into a High-Performance Computing (QC-HPC) installation.
But with all these goals and design intentions, how do you begin to start building it? The answer to that question is far more down to earth…
Large-Scale Models for Large-Scale Platforms
The process of designing and building a large-scale system such as KIDE is naturally complex. It’s one thing to have the design down on paper, but often it’s hard to get a true sense of how the design works until you are able to see it.
To get a sense of what KIDE would feel like in use, we first built a life-sized wooden model of the system. This was important to test the designs the access options and give an indication of what it would be like to work with in real life. After building the full-scale model, the physical size of platform surprised some of the people working on the project:
“Before I joined the project, I saw some illustrations, but there was no human for scale. So, as many people probably did, I thought that it would be relatively small — just like a regular fridge. I was really impressed when I saw the size of it,” our R&D Scientist Jean-Philippe Girard remembered.
Having the life-sized model allowed the team to get a real sense of how the system would be constructed and how people would actually use it. This was a vital step that would inform a lot of the manufacturability choices.
When you’re building something as complex as KIDE, you don’t want to make mistakes that would affect usability in the final production model. This life-sized wooden KIDE would prove invaluable for the construction of the first prototype.
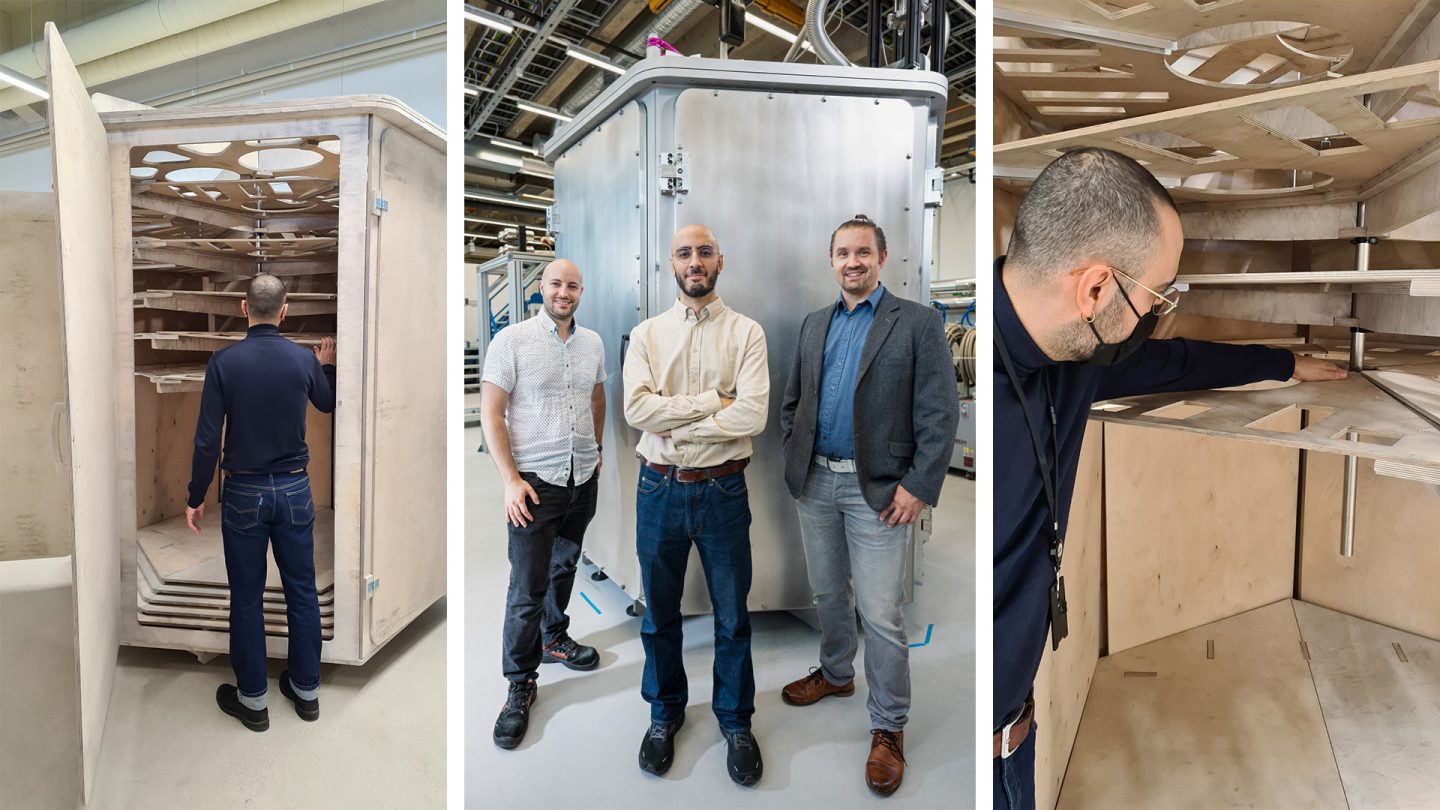
From Wooden Model to Functioning Platform
The KIDE Cryogenic Platform was announced at the APS March Meeting in 2022 — barely a year after the concept was first imagined. This rapid development pace continued during the construction of the first fully-functioning KIDE, which was completed later in the same year.
The first KIDE built was a production testing prototype, created to help determine what was working and where further improvements were needed. For example, the prototype system helped the team better understand the impact of decoupling the condensing pulse tube from the customer payload. Also, being able to stress-test the system by applying a large headload helped them identify any operational bottlenecks in the design.
Once a working platform was up and running, we were able to see the real benefits of KIDE in practice. While the size of the system meant that some work had to be done at height (such as installing the three cryostats), at the same time the design made working on the everyday parts of the system extremely easy. Our Senior Cryo Engineer, Aymeric Mommaerts, adds, “You sometimes need a lift while working, but actually reaching the Mixing Chamber Flange is quite easy as it’s at human height.”
The simplicity of working on a system with a self-supporting vacuum chamber was immediately obvious. Our team could just open doors, remove the radiation shielding, and then have quick access to the system. This accessibility would prove to be one of the many features that make KIDE the large-scale platform of choice for Bluefors’ customers.
Delivering the First KIDE Cryogenic Platform
In April 2023, the first KIDE Cryogenic Platform was ready to be delivered to its new home at IBM. As KIDE is the largest system we have ever designed, delivering such a system comes with its own unique considerations. How do you ship a product weighing 5.7 tons?
While it’s always possible to ship large products via sea, our team discovered a faster alternative, with one transatlantic flight available each month with the capacity to house something as large as KIDE. Within a matter of weeks, KIDE was on a flight to its new destination.
The amount of time it took from initial concept to a final functioning product often surprises people. In just one year, KIDE went from wooden model to customer installation. Bluefors’ Founder Pieter Vorselman tells us, “This is surprisingly fast to go from concept to shipping to the customer. This is something I’m really proud of — that the team actually has achieved this. It was not very easy to do, but anyway we did it!”
The speed of this process has only been made possible through Bluefors’ expertise in both research and development, and in production efficiency, enabled through our industry-leading facilities in Helsinki.
We’re excited to see IBM using KIDE, and its wider adoption in large-scale quantum computing. We can’t wait to see how it’ll be utilized in the future by other cutting-edge quantum leaders.
And if you’re wondering what happened to the wooden model… It’s currently being used as a children’s playhouse!
Learn more about KIDE Cryogenic Platform from our webinar or contact our Sales Engineers to know more about the possibilities it provides.