Installing Cryogen-free Dilution Refrigerator Systems Remotely
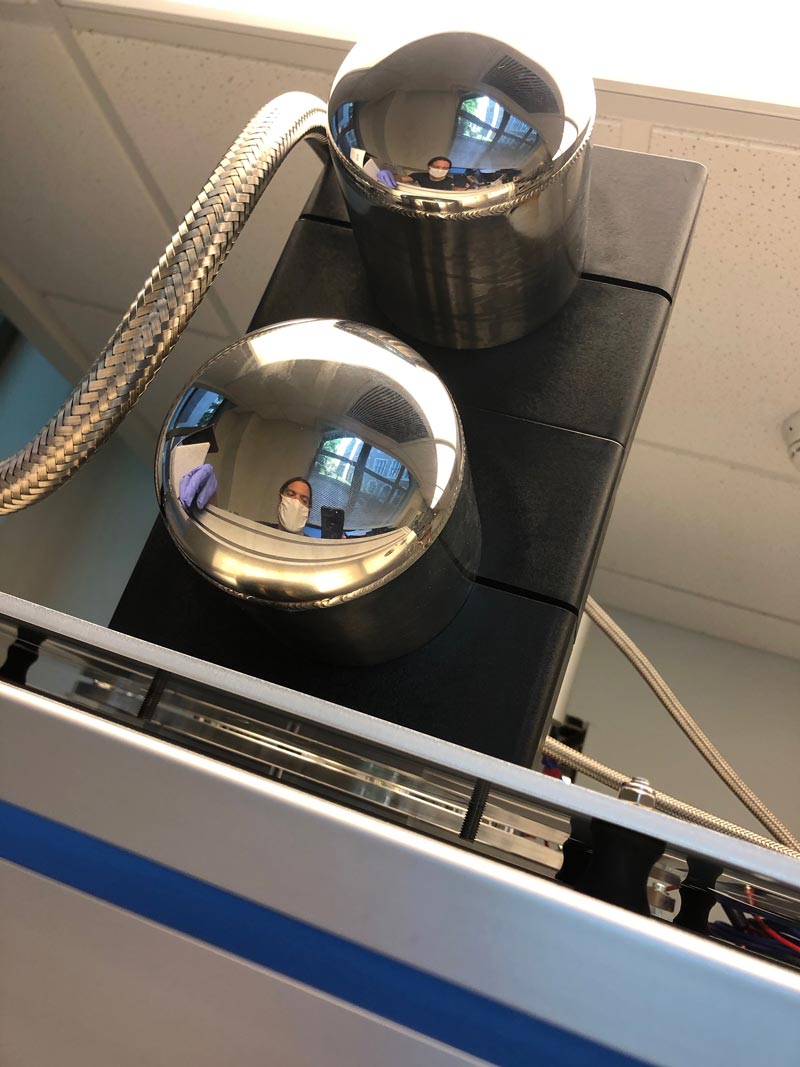
We have started installing our cryogen-free dilution refrigerator systems remotely since May 2020 due to the COVID-19 outbreak, and this tour de force has enabled our customers to continue their work in the laboratories during these unusual times.
Usually, when commissioning a dilution refrigerator system, our Cryo Engineers spend days onsite in the labs with tools in hand, assembling the system making sure that everything goes fine, guiding the customers in the process. In a remote installation, instead of the usual installation days we have online meetings with the laboratory staff who have received our instructions and videos in advance.
We have structured our remote dilution refrigerator installation instructions chronologically, starting from the unboxing of the dilution refrigerator system to building the frame, and so forth. Video links and QR Codes (QR Codes are a registered trademark of DENSO WAVE INCORPORATED) makes it easy for the local laboratory staff to browse through the installation videos, which are arranged the same way as the written installation manual.
When our customers have questions during the remote dilution refrigerator installation, we have dedicated Cryo Engineers answering them. We give full installation support and are available for the time the remote installation takes place. The communication during the installation includes exchange of news in writing or over the video phone calls. Not being present in the lab during the installation is certainly different experience, for everyone.
When the remote installation work has been completed and we know that everything in the system works, our Cryo Engineers report feeling the same pride as on an onsite installation. This is not an easy piece of equipment to make work reliably, but we are putting all our efforts in so that our customers can continue to do their amazing research.
Although installing dilution refrigerator systems remotely have been a good experience, and as much as we have liked working with you remotely as well, we hope to see you all in real life soon.

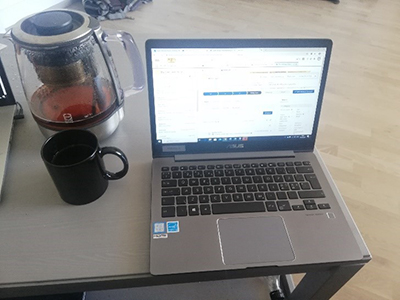
A remote installation story
by Kater Murch, Associate Professor, Physics Department, Washington University
Nothing was going to be normal about installing the dilution fridge during a pandemic lockdown. In fact, a month ago, when the boxes were to be delivered, the campus was fully closed. And so, with that “can do” attitude of an experimental physicist, I went in to help unload the packages myself. Experimental work is always dangerous, but perhaps most so when you don’t expect it. An unfortunate accident while operating the loading dock leveller resulted in a trip to the emergency room, followed by surgery, leaving my left hand’s fingers significantly shorter than they originally were.
Day 1
It used to be that if you want to work at cryogenic temperatures you basically had to devote your whole PhD to building and maintaining a dilution refrigerator. I encountered some of these home-built dilution refrigerators back in my PhD at Berkeley. The fact that you can buy a dilution refrigerator, one that you basically plug in and it gets cold, with seemingly no trouble at all is pretty amazing. I believe that has played a big role in the prominence of microwave frequency quantum systems in the quantum information community. Despite the impressive engineering, these are very complicated machines, and setting one up is filled with day after day of patient and careful work.
Throughout the morning our designated Bluefors’ Cryo Engineer Niko-Ville and I chat. He has a very mellow demeanor, sitting at his desk at home, patiently watching me struggle with this or that. Is he content because he knows that he does not have to struggle with the snakes of hell – that is, the obscenely long high-pressure helium lines for the pulse-tube compressor, which are always a struggle to move into place? Or is he somewhat sad because he is missing the fun? Niko-Ville has no choice but to listen patiently to my stories while I make the connections.
Before signing off for the day, we discover one problem – it appears that one valve does not respond – something that we will have to troubleshoot in the days ahead. There’s always something to troubleshoot.
Day 2
In the early morning we begin leak checking the refrigerator. But where is the leak checker? Frantic 6 AM emails to the department… Fortunately, someone over the age of 40 had borrowed it and so he’s awake at 6 AM to direct me to his lab.
Next, we consider the third stressful step; transferring the very precious helium-3 into the dilution refrigerator. It comes in a bottle with a volume of approximately half a liter and so its pressure is something like 36 atmospheres – high pressure. And we have to get this high-pressure gas into the fridge at low pressure without leaking any of it into the room. After raiding my colleague’s labs of CGA 580 fittings and Swagelok parts, Johanna and I begin to assemble a long contraption of connectors and needle valves and even more connectors.
Day 3
Troubleshooting. Early morning, time to try to solve the problem with valve 2. We open up the back of the control unit. The relays for valve 2 are in the upper left-hand corner of the board. After swapping and switching different things, we conclude that the problem is upstream of the actuators – something perhaps still in the relay board. Nikko-Ville suggests we try swapping some of the other components on the relay board. I gently pry the first one out – it’s an eight-pin integrated circuit – a sneaky little spider of an IC – and it has one of its legs tucked inside, not making a connection. We have no idea how this pin became bent and disconnected since the fridge functioned perfectly on the factory floor in Finland. What a tricky little place to hide a problem.
Johanna is happy that we encountered some of these problems because it means that we get to dig in deep – understanding the systems inside the fridge.
Day 4
At 7 AM we converge on the lab ready for the task of transferring the helium-3 into the fridge. It’s nice to have thought about this for a couple of days because it’s kind of tricky. Johanna and I quickly set things up, and the leak check looks good. Fortunately, the door to the pump room is right by the control unit so we can see the gauges as I gently (actually with all my strength) open the helium-3 bottle. At some point the pressure starts to rise rather quickly, and then I throttle back. Trying to hold the pressure at nearly 50 mbar, we slowly fill the helium into the tank.
So, with the fridge full of helium, feeling satiated after a delicious meal of expensive gas, we ready the fridge for the pulse precool and condense steps. It’s just a few easy keystrokes to start the control scripts and Niko-Ville and I watch the pressures for a moment, discussing how one can check for a block in the impedance by looking at how certain pressures go up at certain rates – every little discussion builds a little bit of intuition into the operation of the fridge. I head home for a quick Zoom meeting with a colleague and then return before lunch to start the condensing script. Again, Niko-Ville and I discussed the pressures, everything looks fine. Back home for lunch I keep an eye on the fridge using TeamViewer.
After lunch I turn on the heat for the still, returning in the afternoon to see that the fridge is slowly churning below 7 mK. Very good, things are working well.
Reflecting on the week, I’m tired from many mornings waking up earlier than I usually would. It feels great. My students are so excited to start research with samples in the coming weeks. I regret that I couldn’t take more of them on this journey, sharing in moments of one-on-one instruction and the excitement of troubleshooting problems and then fixing them.
