Gas Handling System Gen. 2 – Designed for Performance
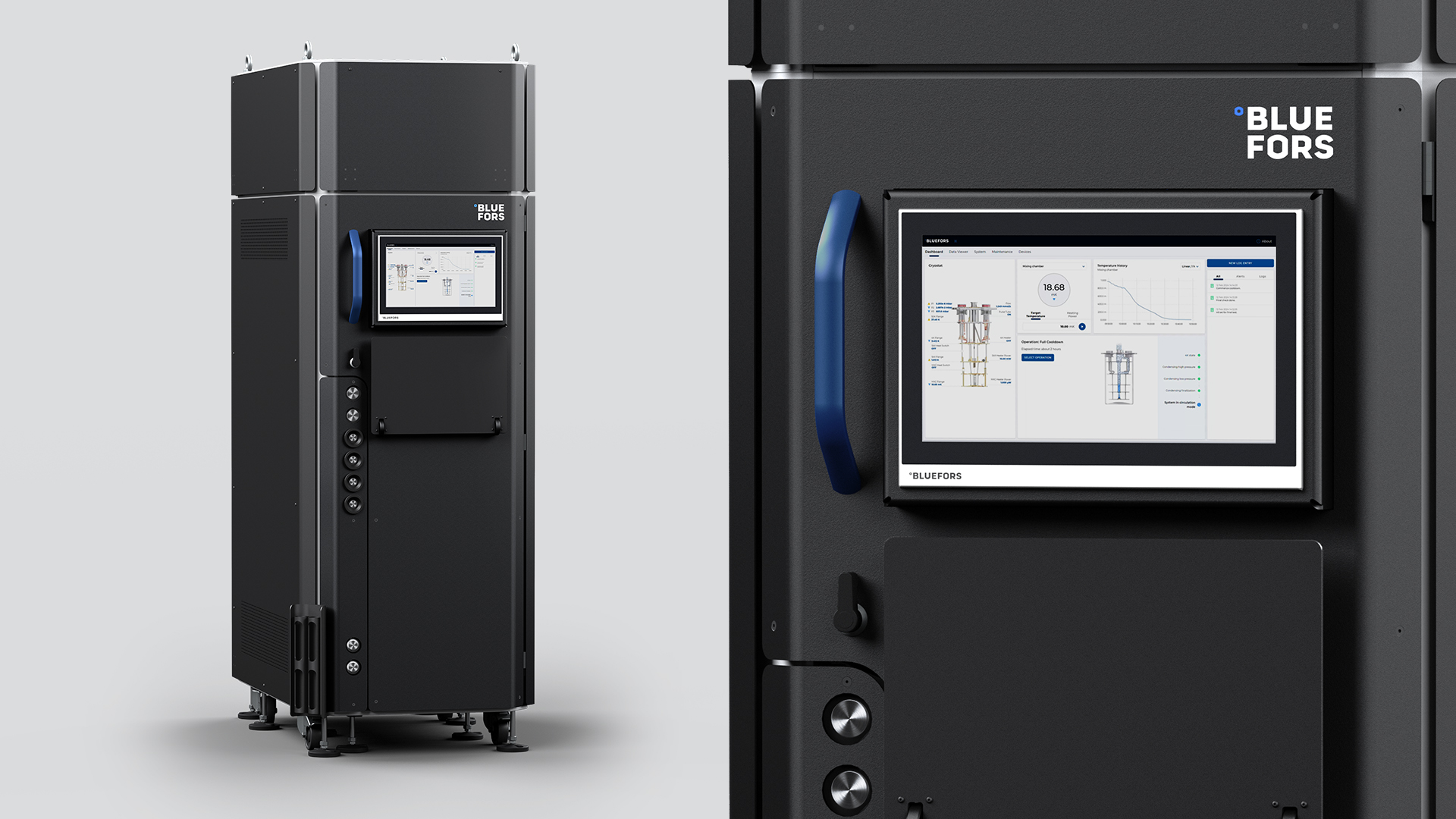
The launch of our new Gas Handling System Generation 2 was the culmination of several years research, development, and design, all focused on utilizing the latest industrial solutions to deliver a powerhouse Gas Handling System to serve our customers well into the quantum future.
The system was designed specifically to meet – and exceed our customers’ needs, as well as taking advantage of the latest components and technology improvements. Now that the first systems have been in customers’ hands for several months, we take a look at the ways Generation 2 Gas Handling System transforms and enhancing the experience and operation of Bluefors Dilution Refrigerators.
Hassle-Free Performance, For Life
Bluefors systems are used in highly demanding environments around the world, and each customer has a specific set of needs that the Gas Handling System and Dilution Refrigerator must meet reliably and consistently over the lifetime of the products.
Our goal with the redesign was to not only maintain our benchmark reliability, but to improve the experience of using the systems, from setup to operation and maintenance.
Simpler set up, right from the start
When you order a new cryogenic measurement system, you want to put it to work as soon as possible. With the enhanced configuration options provided in the all-new control software, we are able to configure and test every system to your specifications in the factory before it is shipped. Once it is installed, you can get to work using your Bluefors system straight away.
More uptime. Less maintenance.
You need your cryogenic measurement system to operate reliably all the time. That’s why Gas Handling System Generation 2 utilizes the latest and greatest components designed for harsh industrial environments. We utilize a new Programmable Logic Controller (PLC) to drive the system and deliver comprehensive built-in system diagnostics for key components. The automated diagnostics ensure any issues are detected before they become problems, resulting in less downtime and reduced maintenance costs.
Say goodbye to tip seals
By far the most common request for our original system was to replace the scroll pump . With Gas Handling System Gen. 2, we’ve introduced a far more durable, low vibration, multi-stage roots pump providing 6 years maintenance-free operation, and eliminating tip seals completely.
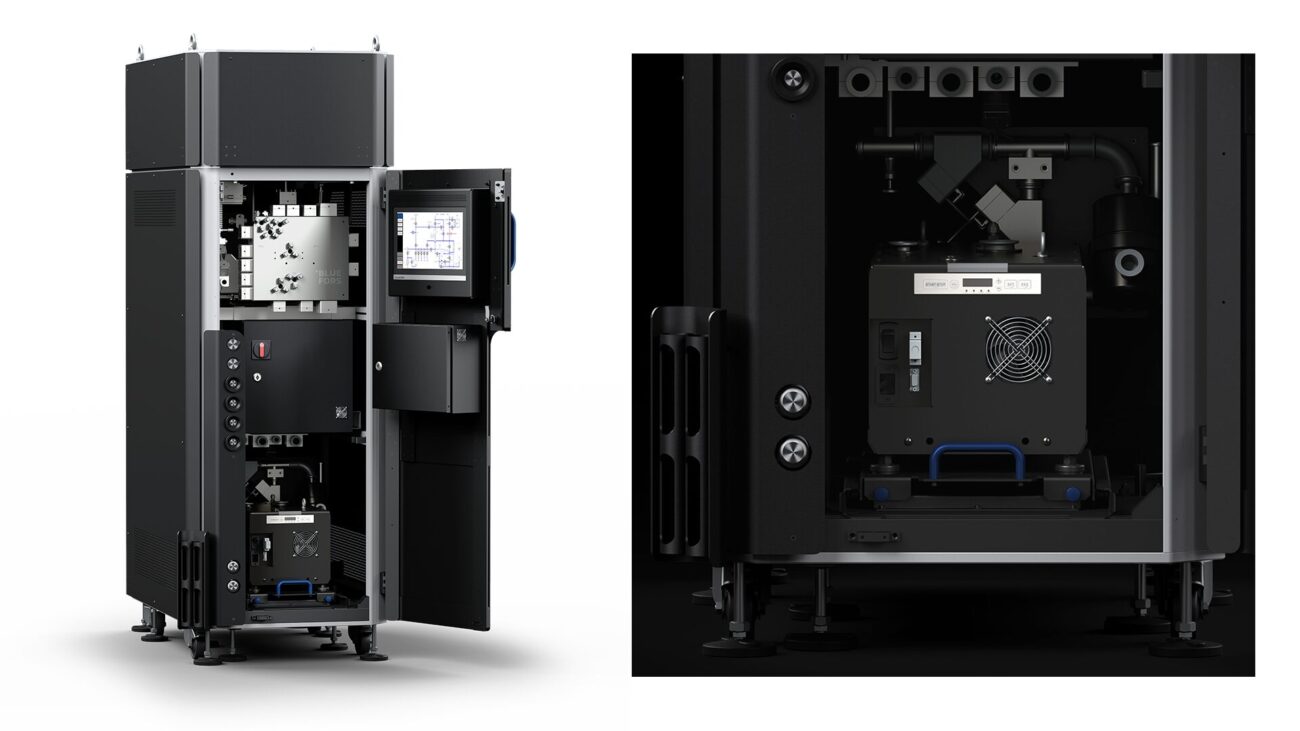
“Gen. 2 is so easy to install – the new design with status LEDs and the ‘fridge door’ is excellent.”
Pilot system user
Safer. Simpler. Quieter.
With highly technical industrial equipment, it’s vital to ensure that all aspects of the system meet safety requirements. Bluefors systems are operated by people with a wide range of expertise, and safe operation is as important for their wellbeing as it is for the system in general.
Certifiably safe
Meeting safety certification standards is an important factor when choosing a system. Certifications not only provide peace of mind, but also contribute to meeting the safety requirements of larger installations into which Bluefors systems are integrated (for example, High Performance Computing centers).
We designed the new Gas Handling System with comprehensive, class-leading safety in mind, and the system has all the required electrical and electromagnetic compatibility (EMC) certifications. The system passes all tests for mechanical and electrical safety under the CB Scheme, and all tests for electromagnetic emissions.
For the end user, this means a lower risk of electrical failure, less disturbance to other lab equipment, more visibility and control over components, and ultimately greater system longevity.
System awareness
When operating sensitive equipment like a dilution refrigerator, you need to be confident that every element of the system is working as expected. Gas Handling System Gen. 2 takes cryogenic state awareness to the next level with ambient temperature logging , compressed air and cooling water sensors, valve position awareness, and power consumption measurement at the individual component level. Dedicated safety devices and circuit breakers protect the system, and an uninterruptable power supply (UPS) provides backup security for the PLC.
Accessible control
Labs often have users with different levels of expertise, and operating the new GHS can be as simple – or as detailed – as you need. For users that need to monitor internal components, GHS Gen. 2 makes this easier than ever. The ergonomic door offers easy access to all primary hardware such as PLC display, roots pump, valves, and sensors.
Low noise (of all kinds)
In a lab environment with sensitive equipment, the last thing you need is noise – of either electromagnetic or sonic varieties. As already mentioned, the system passes all electromagnetic emissions tests (and shielding on the cryostat vacuum cans helps protect your samples).
When it comes to audio disturbances, the new frame and panel design help to keep the decibels down. Inside the Core Unit, we’ve added pump silencers, and the new multi-stage roots pump operates at near silence. Your ears, and your experiments, will both be happy.
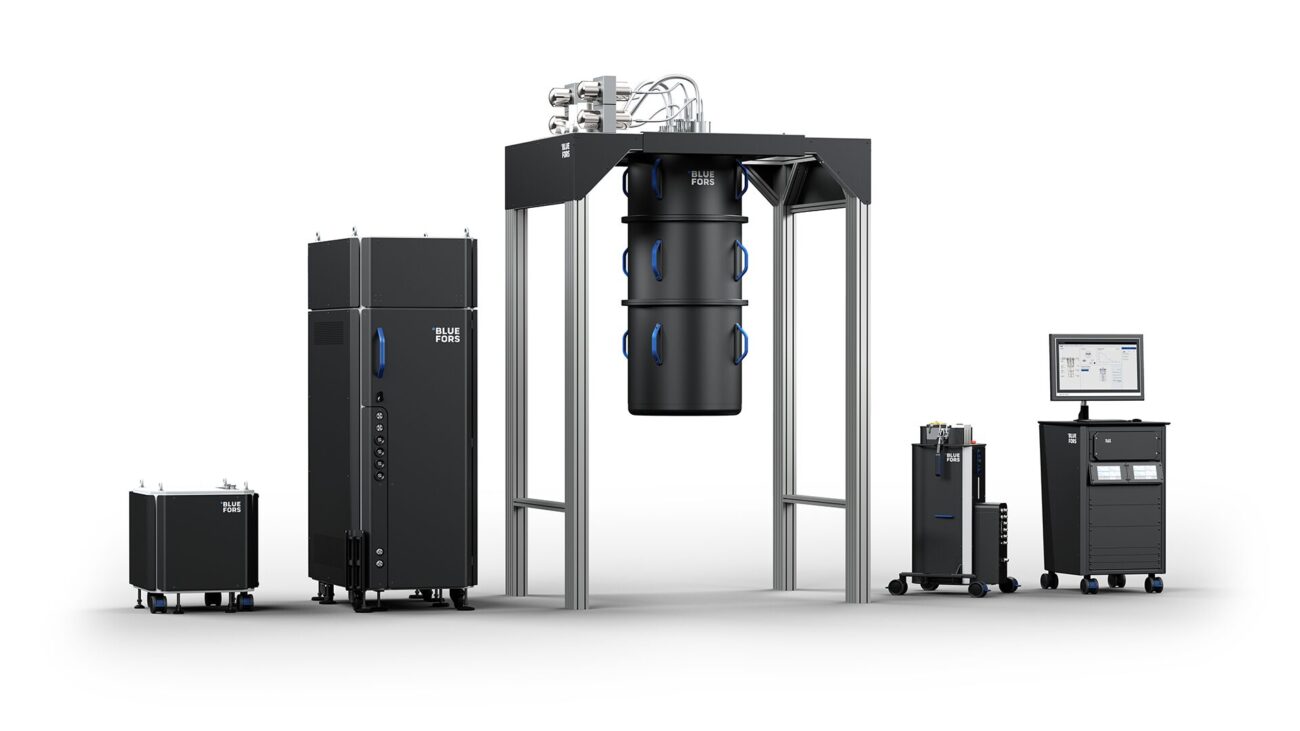
“GHS Gen 2 is miles ahead of our previous experience.”
Pilot system user
Cutting-Edge Performance for Cutting-Edge Science
Quantum technology is really at the forefront of scientific research, and you deserve a system that delivers unbeatable performance to help you get the results you are seeking. And while a cryogenic measurement system is an undoubtedly complicated tool, our advanced Control Software makes operation a piece of cake.
Uninterrupted operation
When conducting long-term, sensitive experiments, the last thing you need is a critical failure that derails your research. The modular Gas Handling System Generation 2 can help to alleviate these worries with additional redundancy features such as a Dual LN2 Cold-Trap, turbo bypass valves, and an optional Redundant Main Circulation Unit.
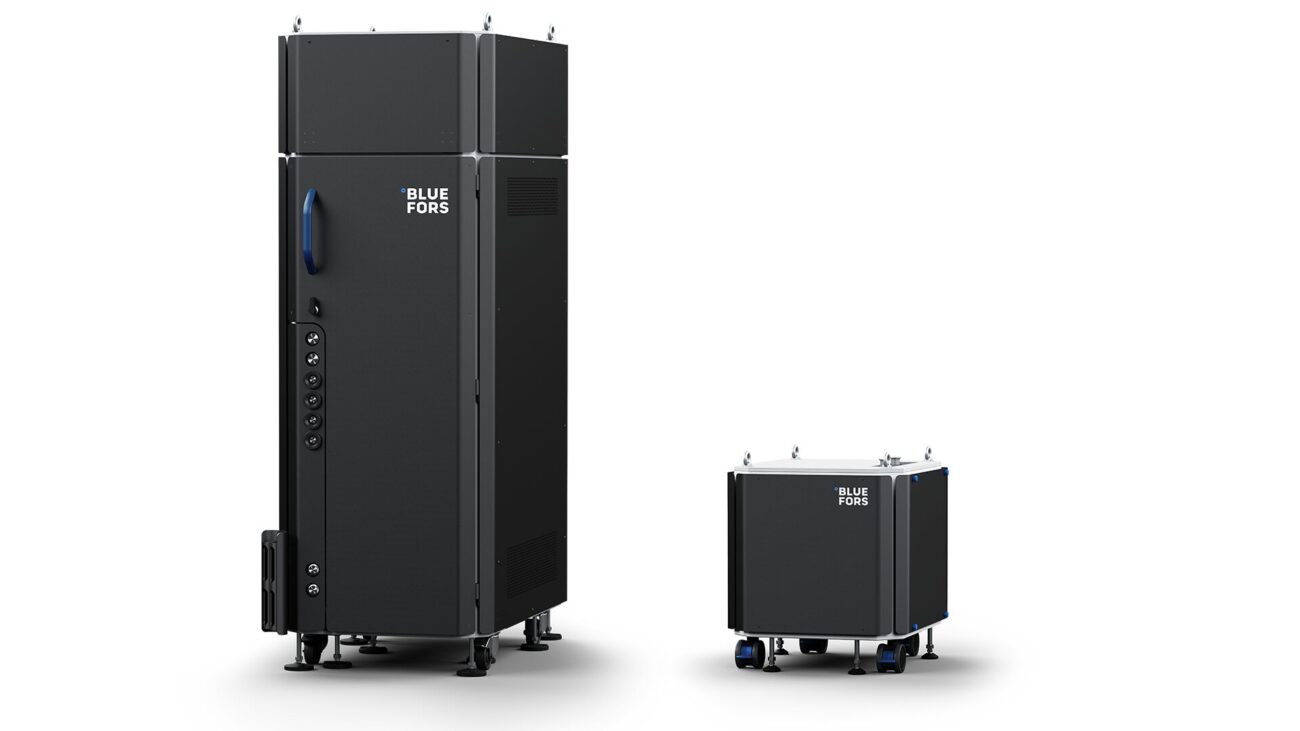
Next Generation Control Software
A powerful system demands powerful software. Users told us they wanted a deeper level of control and insight into the cooling process, so we completely redesigned the Control Software. Users can easily initiate a fully automated cooldown sequence with a single click. Users can easily create graphs tracking a vast array of data points utilizing detailed logs of components and system operations. More experienced users can take full control of the system at a more granular level via API.
Diagnostics and alerts
Full diagnostics, and remote operation via the Web UI offer intuitive, powerful control over your system, wherever you are. If there’s a problem, built-in automatic alerts and notifications will let you know. The internal IPC also features maintenance profiles for all key components, so you get full observability of the entire system. (Read more in our Control Software Gen. 2 blog)
“The new software is considerably better – the data viewer is super helpful. It feels like a modern world now!”
Pilot system user
Designed for every use case
Different labs have different requirements, architecture, and layout options – so there is no one-size-fits-all solution. To solve this problem, we created a modular design that can be adapted according to each customer’s lab environment specifications and needs.
Configure it your way
Limited by low ceilings or trying to fit into a tight space? No problem. The GHS can be configured as a fully integrated unit, or with key components mounted on the ceiling, or placed separately on the floor. Additional hardware, such as the Redundant Main Circulation Unit, Thermometry Unit, Instrument Cart, and door- or table-mounted screen provide additional application flexibility.
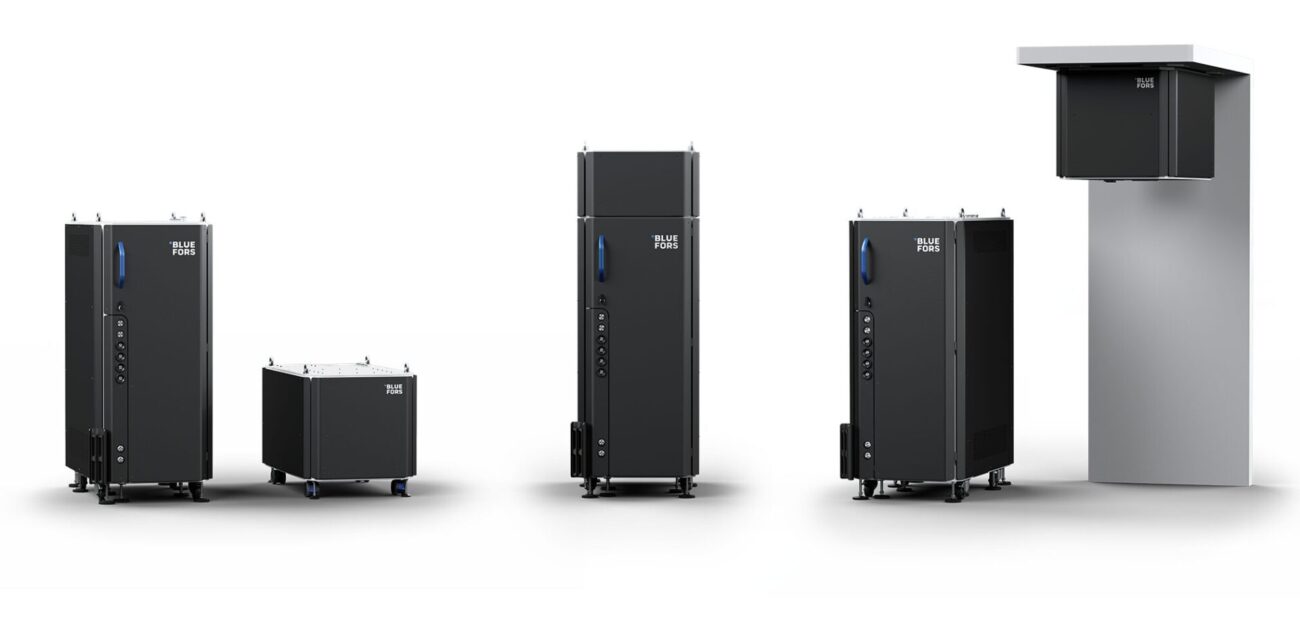
Fast turnaround
To speed up experiment turnaround, we’ve also updated our Fast Sample Exchange system. It can be fully operated via the Control Software for easy, automated access to your experiments without the need to remove the vacuum cans. The FSE also features an accelerated sample warm-up feature to ensure additional safety and faster exchange of samples, a LED position indicator, and emergency stop button.
Ergonomic touches
Sometimes it’s the small things that make a big impact. Removing vacuum cans and shields from the cryostat has always been a simple operation, but nonetheless we wanted to improve the ergonomic experience by improving handle placement and making other small changes that make everyday interaction with the system easier.
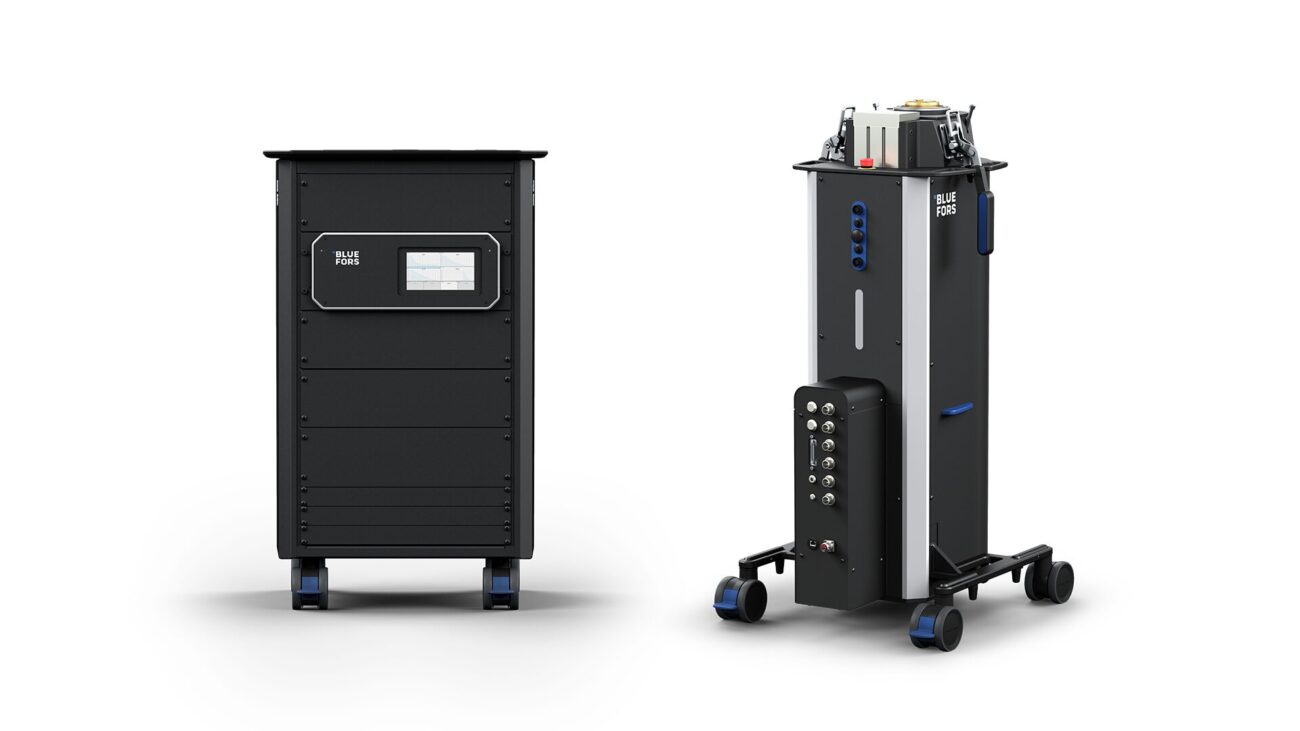
Power to Deliver the Quantum Future
With rapid advances being made in the quantum technology, we wanted to develop a next generation Gas Handling System that addressed the more demanding needs of customers today and in the future. Our huge user base of over 1400 existing systems helped us gather feedback and inspiration for improvements that would cater for a wide variety of industrial applications at different scales.
Gas Handling System Generation 2 delivers high performance through cutting-edge features. Its modularity makes it more flexible and more easily adaptable for different customer use cases. Providing longer system lifetimes and class-leading safety, it combines incredible power with unprecedented ease of use for every user.
Learn more about the Gas Handling System and Control Software on our website, or contact sales for more information.