Heat Recovery System Installed at Bluefors, Transforming Heat from Waste to Resource
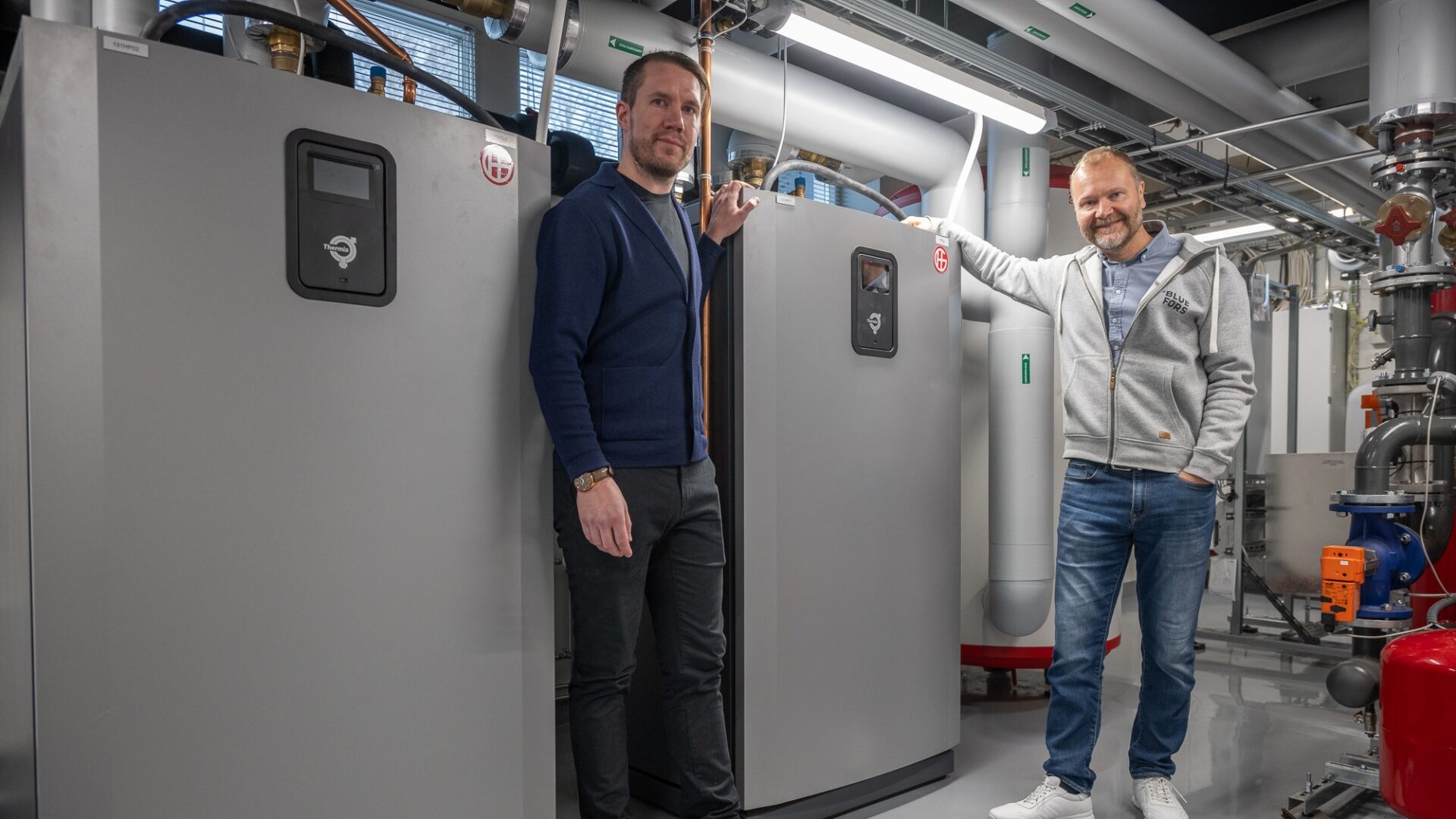
In our facilities here in cool Finland, heating our workspaces and domestic water is a year-round necessity. However, we also continuously generate heat as a by-product of our production processes, and this has typically been dissipated outside. To remedy this waste, over the past summer we installed a heat recovery system; by using heat pumps, excess heat from our water-circulation cooling system is now redirected to provide our facility heating needs, warming both our workspaces and water.
This system allows us to decrease our reliance on district heating, lower our energy consumption, and importantly, reduce our energy use emissions by up to 35%.
Heat Generation in the Cryohall
All facilities produce some heat, but not necessarily significant amounts of it, and often not all year round. For example, convectors used to cool rooms also produce heat as a by-product, but only in the warmest months when cooling is used the most. However, our facility is different. Our Cryohall – the space where we manufacture our dilution refrigerator measurement systems – generates heat continuously, no matter what the season.
The main sources of heat in the Cryohall are the dilution refrigerators under testing, and more specifically: their cryocoolers. The two core components of a cryocooler are the cold head (located inside the dilution refrigerator) and its compressor. When a dilution refrigerator cools down, the cryocooler components power the largest drop in temperature: from room temperature down to approximately 4 kelvin.
To achieve this cooling effect, the cryocoolers extract heat energy, leaving behind only extremely cold temperatures, and consequently generating heat as a by-product. This heat accumulates in the cryocooler’s compressor, and is transferred, along with the compressor’s cooling water, to our building’s cooling network. Excess heat is then typically discarded via condensers – releasing hundreds of kilowatts of heat outside of the building.
Recognizing the potential of this waste heat, our Facilities team initiated a heat recovery project with the goal of re-using the generated heat energy for the facility’s heating purposes. The heat recovery project began in June 2022, and after a year of planning, the system was successfully installed in 2024.
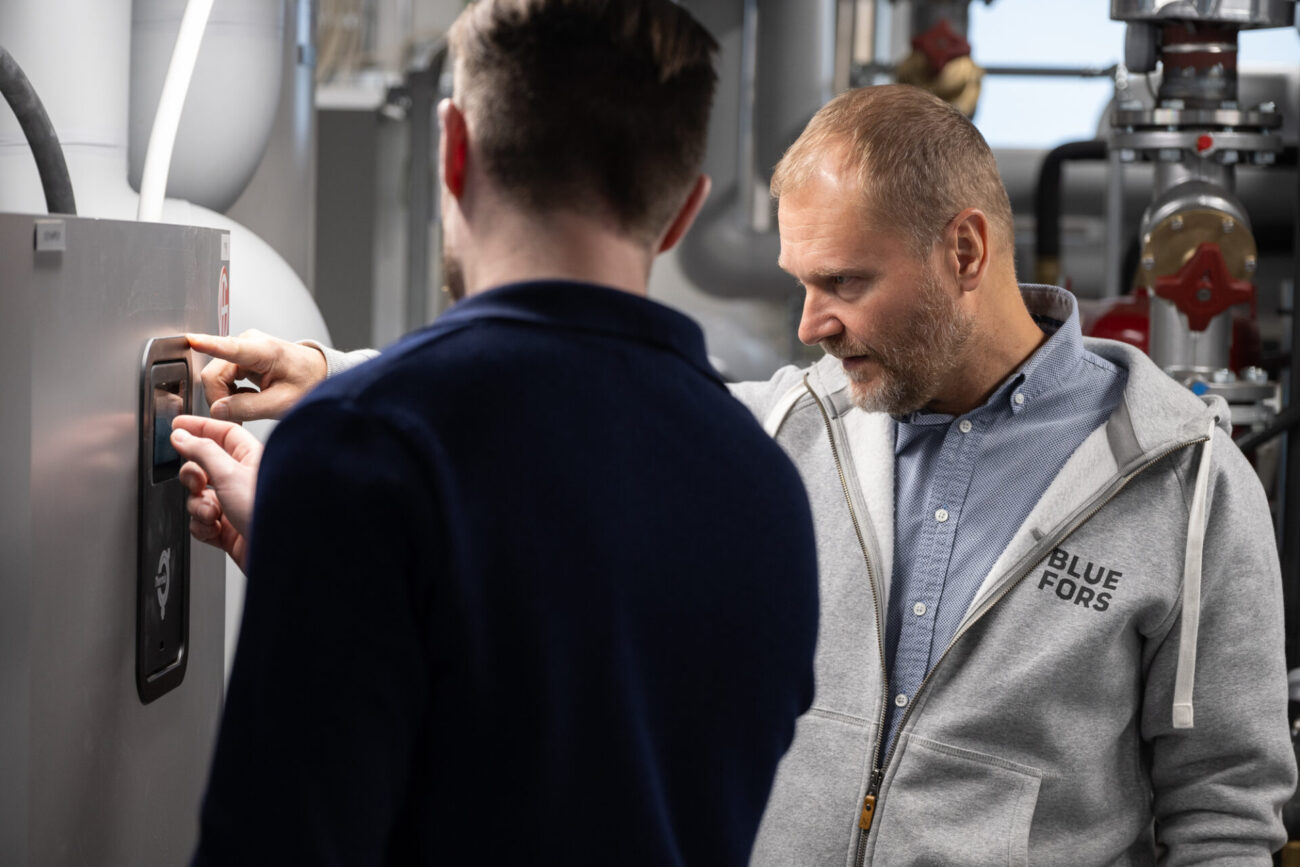
How Does the System Work?
The water-circulation cooling network in our building provides cooling for the cryocooler compressors in the Cryohall and the convectors (for cooling spaces). The compressors and the convectors receive cold water and, as a result of heat transfer, expel warm water. The main function of the cooling network is to extract the heat from the water, and return it cool to the Cryohall and the convectors.
Previously, this process was carried out using water cooling units that pushed the water to the condensers. The condensers transferred heat from the water to the surrounding air, effectively cooling the water so it could be circulated back into the cooling network.
With the new heat pumps, our produced heat can be repurposed for our own heating needs. The heat pumps – similar to the water-cooling units – receive the excess warm water, cool it again, and circulate it back into the cooling network. However, instead of dispersing the heat outside the building, the heat pumps direct it into our central heating and domestic water heating.
With the new heat pumps, our reliance on condensers and district heating is significantly reduced.
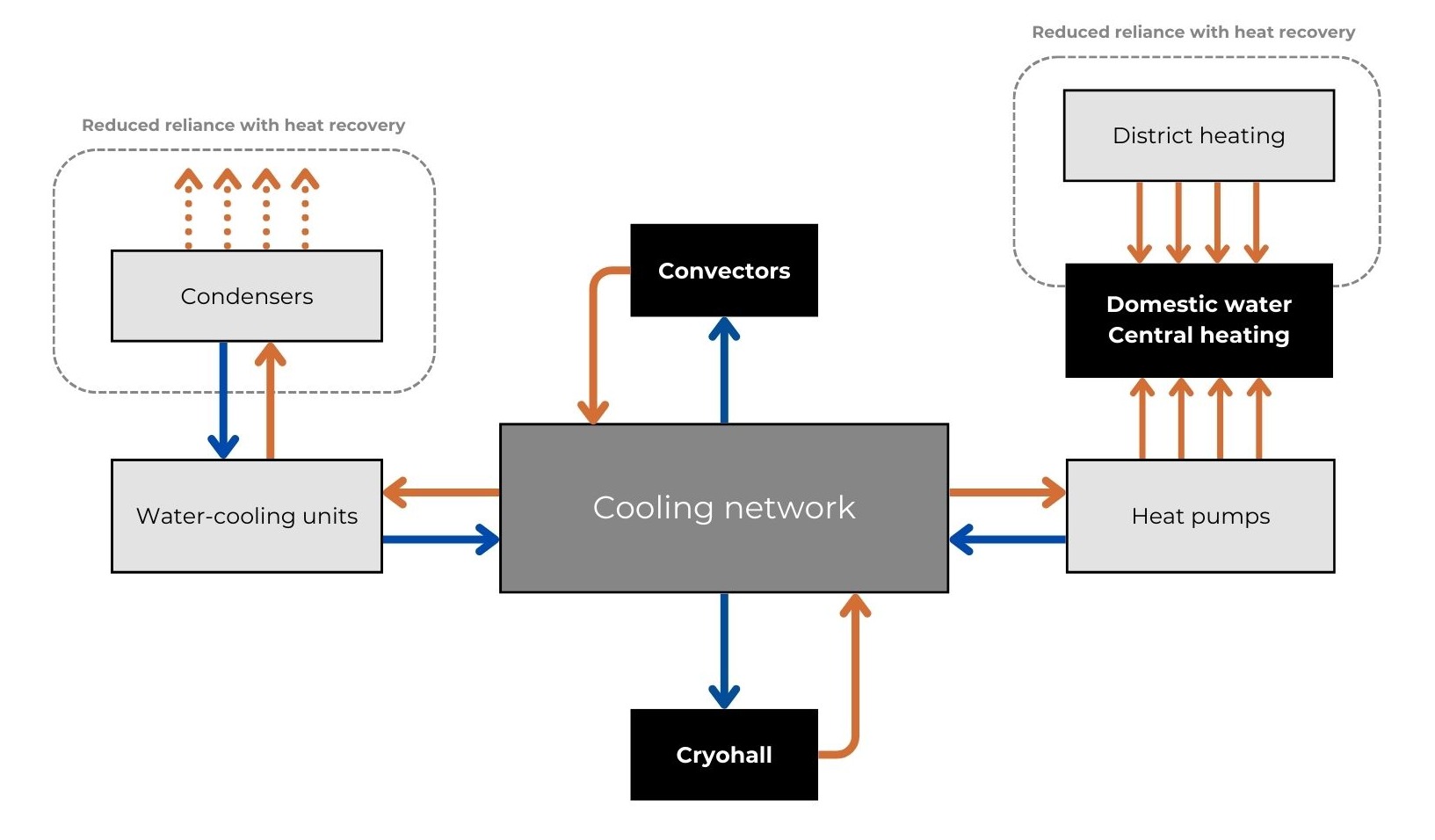
Meeting Heating Needs
The new heat pumps will cover all the domestic water heating needs of our Helsinki facility during the warmest months, typically from April to September. This means that during this period, district heating, a significant source of emissions, is no longer needed.
Domestic water, which includes tap water used for drinking, washing hands and dishes, and taking showers, arrives at a temperature of approximately 5° C. This means that almost all water requires heating. While this might not seem substantial in household water use, the heating demand becomes significant when the water use of the 400 people working in our facility is combined. For example, after just one month of operation, the heat pumps had heated about 120 cubic meters of water from 5° C to 60° C – all with the by-product heat from our processes.
The next steps in developing the heat recovery system involve connecting the water-cooling units and heat pumps so that the systems can communicate. With a unified system, the water-cooling units will not cool the water if the heat pumps are meeting all the cooling needs. This upgrade allows the water-cooling units to automatically adjust to the heat pumps’ capacity, ensuring consistent energy use without overcooling or underutilizing resources.
The heat pumps are also designed with an adjustable 200 kW capacity, with an additional 100 kW upgrade option available, ensuring the system can adapt to future demands and continue to operate efficiently.
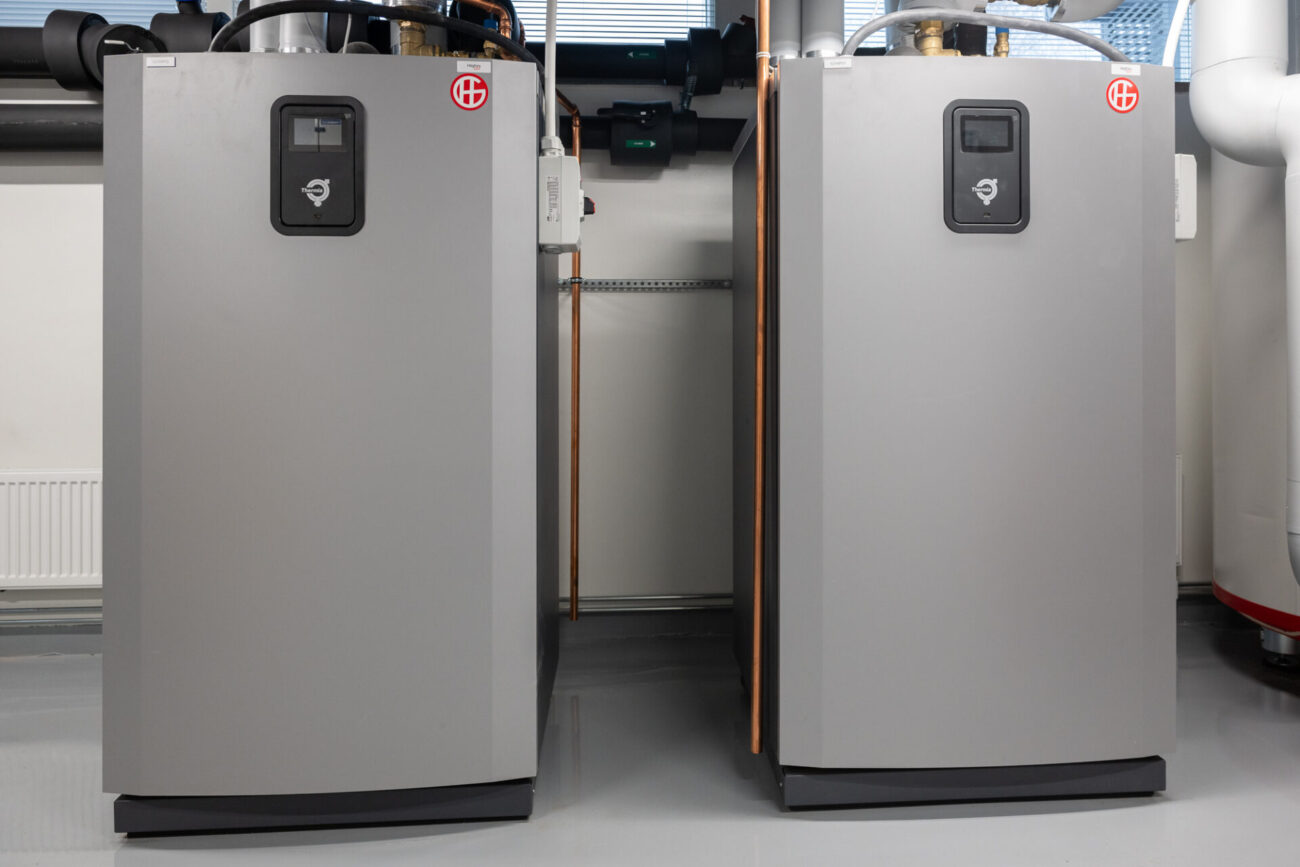
Reducing Emissions with Heat Recovery
Reusing wasted heat delivers cost savings, but the greatest benefit of the heat recovery system is the significant reduction in emissions. Now, our facilities rely less on district heating, which accounts for a significant fraction of our energy consumption. The heat recovery system reduces our energy consumption by approximately 30% and reduces the emissions from energy use by up to 35%. So, while energy is still needed to power the system, the efficiency gained means we can cover significantly more of our needs with the same amount of energy.
When quantified, the recovery and reuse of produced heat results in a yearly reduction of 107,000 kg of CO2e. To illustrate the significance of this reduction, the amount of emissions reduced yearly is equivalent to those emitted by driving an internal combustion vehicle 375,000 kilometers (based on the average emissions rate of passenger vehicles, 140 g/km). That is like taking a road trip around the globe 9.4 times! Or, if you prefer a more cosmic comparison, it’s almost the same as driving from Earth to the Moon.
As these illustrative examples show, the heat recovery system has a tangible impact on the carbon footprint of our energy consumption.
A Step Towards Environmental Sustainability
To strengthen our environmental sustainability, our overarching goal is to reduce our greenhouse gas emissions across the entire value chain. To effectively reduce emissions, we continuously seek opportunities for improvement.
Reducing emissions is by no means a simple task, nor is it achieved with one big leap. Often, effective solutions are responsible decisions that make practical sense – like using excess heat for heating needs – rather than drastic transformations. By taking responsible and proactive steps wherever we can, we are achieving meaningful, sustainable progress.
Learn more about our ongoing work in sustainability from our Sustainability pages.